What can happen if the operations department does actually do the thinking job and decides for themselves?
- Operations people normally think big, which means, the bigger the batch/lot size, the better for the fixed costs degression.
- They are not enough informed about the market and should solely concentrate on production/operations efficiency.
- Being focused on short term production results, they tend to neglect to look at the long term when it comes to planning and forecasting.
- Too many interfaces (inside and outside communication) distracts them from their real job - an efficient operation and delivery on time and in full.
There are more reasons, but these are the most important ones.
And now for future reference, when I say 'operations' or 'SCO', that actually means Supply Chain Operations. This is the department in the supply chain which "does" things, and that can be usually production, distribution, etc...
Initially, this blog was about my life as management consultant. Nowadays, I'm blogging about all sorts - work, politics, religion, whatever comes along and butters my muffin, as they say... And no, one won't see me naked.
Friday 22 May 2009
Thursday 21 May 2009
The Brains and the Hands
Talking Supply Chain I'd like to start with the model. Like in many areas it is advisable to separate the "brains" from the "hands", which means, don't let the doers decide what they should do and how much. That never ends up at an optimum.
In a project I am always open for suggestions and agree happily on some alterations to the model and tools which I intend to implement, but on that issue I categorically stay tough: NEVER LET PRODUCTION DECIDE WHAT, HOW MUCH AND WHEN THEY HAVE TO PRODUCE SOMETHING!!!
In a project I am always open for suggestions and agree happily on some alterations to the model and tools which I intend to implement, but on that issue I categorically stay tough: NEVER LET PRODUCTION DECIDE WHAT, HOW MUCH AND WHEN THEY HAVE TO PRODUCE SOMETHING!!!
Wednesday 20 May 2009
What's now?
What I generally do and did for my client: I would go to a business unit, and they are organised worldwide, analyse the situation, come up with recommendations for improvement, built a business case, and install the improvements. I mainly work in supply chain planning departments, factories and distribution centres.
The countries I have been involved with so far with this client: The Netherlands, Belgium, France, South Korea, China, Hungary, Poland and a tiny bit of UK.
What I want to do from now on in the blog is to write a bit more about the tools and methodology I used in the last couple of years.
Saturday 16 May 2009
Friday 15 May 2009
Nissan, the Team
We had one task force from Nissan during the 2 projects, Peter B (picture above). He was a very good guy and lived in Northamtpon. He knew the company pretty well and helped us installing our new management tools rather swiftly.
In the first project my consultant was Anne-Laure, and in the second one Javier.
Each project lasted for about 4 months.
The main issue was, Nissan was riddled with "cultural differences". There were the Spanish employees in the 2 sites in Spain, the British ones in Milton Keynes, and there were myriads of Japanese employees who were in Europe for a certain amount of time and also included in the project.
I do remember problems with the Japanese. They were language barriers and also no interest at all in any European project, as they were all very focused on directives from Japan.
Thursday 14 May 2009
Nissan Research and Development
One of my last projects with Proudfoot was the one at Nissan R&D in the UK, but with further 2 locations in Spain.
The project was about raising personal efficiencies of R&D directors, and in a second follow-up project a similar approach was rolled down to the supervisors.
The core product was to eliminate non-value added time and add more creativity to the European R&D department.
We did that through coaching, implementing a new "efficient meeting format" and e-mail etiquette. Each meeting was to be fedback and coaching to the chairmen given. The new e-mail formats ensured unity in writing e-mail across the European sites.
In special vision workshops we introduced them to the idea of new creativity at the workplace.
The project was about raising personal efficiencies of R&D directors, and in a second follow-up project a similar approach was rolled down to the supervisors.
The core product was to eliminate non-value added time and add more creativity to the European R&D department.
We did that through coaching, implementing a new "efficient meeting format" and e-mail etiquette. Each meeting was to be fedback and coaching to the chairmen given. The new e-mail formats ensured unity in writing e-mail across the European sites.
In special vision workshops we introduced them to the idea of new creativity at the workplace.
Saturday 9 May 2009
Mazda - Warehouse Management (2)
The warehouse project was actually pretty successful. We implemented fully fledged management systems in all their warehouses, trained management in management skills, implemented relevant KPIs, a planning tool and master schedule, supervisory shop floor tours... Well, the fully monty really.
I never thought I'd ever become an expert in warehousing and distribution. In a later project I was able to deepen my knowledge in that sector even further.
I never thought I'd ever become an expert in warehousing and distribution. In a later project I was able to deepen my knowledge in that sector even further.
Labels:
management systems,
management training,
Mazda,
warehouse
Friday 8 May 2009
Mazda - Warehouse Management (1)
Anyway, what we did with the warehouse section, we thorougly analysed them all. I think they had 5 throughout the country. They were all lacking the same: standards for each activity, good management, daily follow-up on the operation, no planning, no measurement of results... Basically, they had nothing and we had to start from scratch.
Thursday 7 May 2009
Mazda - Organisation
The organisational development bit turned out to be pretty difficult. What we did was to create an "Organisational Brown Paper" where we drew the current organisation in its rather detail.
We also had a list of all the salaries per department, so we could detect the cost per department (and the turn-over).
Then, we did the "green meadow approach", where we sat down and created the "new" organisation as if we were to establish a new company and we could use as many people from the "old" payroll as we wanted. We had several workshops, mainly with the directors and HR.
The final result was a suggestion for a new organisation. Initially, we did not sell the implementation of that new organisation, only a suggestion for a new one.
It sounds very easy, but the main problem was this HUGE resistance of literally everyone. I was greeted with hostility whenever I was spotted somewhere in the building. But we finally got it!
I had a task force. His name was Dominic. He was working as manager in one of their warehouses and he helped me with the organisation and the warehouses.
We also had a list of all the salaries per department, so we could detect the cost per department (and the turn-over).
Then, we did the "green meadow approach", where we sat down and created the "new" organisation as if we were to establish a new company and we could use as many people from the "old" payroll as we wanted. We had several workshops, mainly with the directors and HR.
The final result was a suggestion for a new organisation. Initially, we did not sell the implementation of that new organisation, only a suggestion for a new one.
It sounds very easy, but the main problem was this HUGE resistance of literally everyone. I was greeted with hostility whenever I was spotted somewhere in the building. But we finally got it!
I had a task force. His name was Dominic. He was working as manager in one of their warehouses and he helped me with the organisation and the warehouses.
Wednesday 6 May 2009
Mazda - Car Sales
In the car sales workstream we needed to deal with selling skills of car salesmen in those dealerships around southeast England.
It was a similar programme to the delicatessen one I managed - selling skills, upselling, more-selling. We trained them, played mystery shopper, had a training film, coached them, etc...
And as usual in projects like these it was a TTT approach, where we trained the trainer (TTT) and the trainer (the local car dealership managers) trained their sales staff. The board director was part of a film where he had to "send out the message" about the project, etc.
That whole workstream was pretty successful. I was only vaguely involved as my collage Judith was responsible for that work stream.
Unfortunately, I do not have too many pictures, in fact close to none, of this project.
It was a similar programme to the delicatessen one I managed - selling skills, upselling, more-selling. We trained them, played mystery shopper, had a training film, coached them, etc...
And as usual in projects like these it was a TTT approach, where we trained the trainer (TTT) and the trainer (the local car dealership managers) trained their sales staff. The board director was part of a film where he had to "send out the message" about the project, etc.
That whole workstream was pretty successful. I was only vaguely involved as my collage Judith was responsible for that work stream.
Unfortunately, I do not have too many pictures, in fact close to none, of this project.
Tuesday 5 May 2009
Mazda - UK!
After that year with Otto Bock, I finally got a project in the UK. My first proper job there since I started my career and moved to London. We are in the year 2002 now.
I was on a project in Tunbridge Wells, with a Mazda spinn-off. The project had 3 parts: car sales, organisational realignment and warehousing. My part was the organisation and the warehouses.
The client was a difficult one. The chairman was from Japan, there was an English CEO, and several English board members. There were constant frictions between chairman and CEO. I can talk that openly as this company does no longer exist.
The chairman was rather "tough" when it came to organisation, the CEO was more "soft" but also unreliable and sometimes with outbursts of verbal violence. A tough cookie!
The board of directors was also extremely difficult to deal with, especially my warehouse director.
I was on a project in Tunbridge Wells, with a Mazda spinn-off. The project had 3 parts: car sales, organisational realignment and warehousing. My part was the organisation and the warehouses.
The client was a difficult one. The chairman was from Japan, there was an English CEO, and several English board members. There were constant frictions between chairman and CEO. I can talk that openly as this company does no longer exist.
The chairman was rather "tough" when it came to organisation, the CEO was more "soft" but also unreliable and sometimes with outbursts of verbal violence. A tough cookie!
The board of directors was also extremely difficult to deal with, especially my warehouse director.
Monday 4 May 2009
Isle of Man
I have forgotten one project. The company was situated on the Isle of Man and produced kettle switches. It was an extremely peculiar project. The local director, a Welshman, had to sleep on a camping site as his company did not want to pay for a hotel; he also had to pay for his flights home every week or fortnight.
And what I have also learned, one ought to wave good-bye to the ferries leaving the island, otherwise it would bring back luck.
Our hotel, the poshest one in town, and an old Victorian one, was the draftiest place on earth with the worst service ever, and beds with mattrasses hanging through to the floor.
We were always scared on Friday afternoons that there was no storm, as otherwise Manx Airways would not leave the airport and we were caught on the island for the whole weekend. Scary thought.
The project as such was rather basic. It was a production project where we improved machine and labour efficiencies. I was responsible for the training and coaching.
One of the managers was a girl called Sue. She was from Liverpool. I had absolutely no clue whatever she said. I just sat there and happily smiled at her and nodded... ;-)
And what I have also learned, one ought to wave good-bye to the ferries leaving the island, otherwise it would bring back luck.
Our hotel, the poshest one in town, and an old Victorian one, was the draftiest place on earth with the worst service ever, and beds with mattrasses hanging through to the floor.
We were always scared on Friday afternoons that there was no storm, as otherwise Manx Airways would not leave the airport and we were caught on the island for the whole weekend. Scary thought.
The project as such was rather basic. It was a production project where we improved machine and labour efficiencies. I was responsible for the training and coaching.
One of the managers was a girl called Sue. She was from Liverpool. I had absolutely no clue whatever she said. I just sat there and happily smiled at her and nodded... ;-)
Friday 1 May 2009
Otto Bock - Final Thoughts
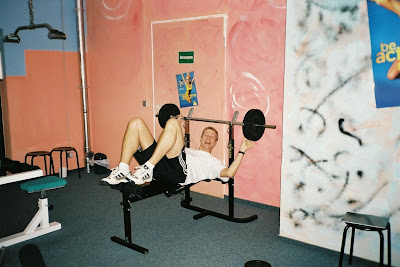
After all, and apart from those special "happenings", and even they were quite good in terms of learning experience, it was a great project. The client was satisfied, the core team was good, the location was nice, I learned a lot, and it formed me as project manager. So far it was my biggest single project, and also my most complex one. It was easy at times, sometimes very difficult, sometimes I wanted to quit my job. Overall, I loved it. And I feel privileged that I was able to be the manager of it.
Subscribe to:
Posts (Atom)