This week I am doing the same as last week in Budapest. It is the same holding, but a different local client; the business is the same, but somehow the 2 sites are completely different.
I am doing the audit - Supply Chain Planning, Supply Chain Operations, and the Distribution Centre.
Initially, this blog was about my life as management consultant. Nowadays, I'm blogging about all sorts - work, politics, religion, whatever comes along and butters my muffin, as they say... And no, one won't see me naked.
Wednesday 9 September 2009
Saturday 5 September 2009
Budapest, August 2009
I visited my client in Budapest for the week and undertook an audit of the management system I installed 2 years ago. The management system basically comprises the 2 main parts - an organisational separation from planning and operations, and the implementation of lean management tools which would help them to manage the operation efficiently.
I am flying to Budapest again in 2 weeks and continue and follow-up on the audit. I am also presenting a tool for stock management which will help them to make their stock situation visible and act accordingly.
I am flying to Budapest again in 2 weeks and continue and follow-up on the audit. I am also presenting a tool for stock management which will help them to make their stock situation visible and act accordingly.
Labels:
A-B-C Analysis,
Analysis,
Budapest,
implementation,
SCO,
SCP
Saturday 29 August 2009
The Bill - Week 4
The training is finally over. I must say it was one of the most intense experiences I have had in a while. Apart from lvarious egal bits we learned how to fight fires and yes, I passed my last exam with 92% which made me smile.
I am very glad I did the course and joined the MET, and I am very happy I managed to pass all exams, practical and academic ones, successfully. Once one is in his late 30ies, learning must be learned again.
The teams of trainers and trainees were great. We had an extremely good time, and with many of them I became good friends. Facebook helps to stay in touch because most of us will be allocated throughout all London boroughs.
Anyway, my real life has me back now. This coming week I am flying out to Hungary where I am going to analyse a company at which I installed a management operating system a few years ago. More of that in a new blog entry at the end of this coming week.
I am very glad I did the course and joined the MET, and I am very happy I managed to pass all exams, practical and academic ones, successfully. Once one is in his late 30ies, learning must be learned again.
The teams of trainers and trainees were great. We had an extremely good time, and with many of them I became good friends. Facebook helps to stay in touch because most of us will be allocated throughout all London boroughs.
Anyway, my real life has me back now. This coming week I am flying out to Hungary where I am going to analyse a company at which I installed a management operating system a few years ago. More of that in a new blog entry at the end of this coming week.
Sunday 23 August 2009
The Bill - Week 3
Week 3 is over and I am absolutely exhausted. Not that the material we learn is overly difficult, but maybe, since it is all new, one feels a bit overwhelmed. Anyway, we got to feel CS gas this week, which was "interesting". I got a full load blown right into my eyes by the wind when they sprayed it. And then I was blinded for a while. One thing is for sure, it is a good and effective tool.
And then we had 2 days of life saving training. That was extraordinarily good and important to have. Thinking about my last first aid training, which was back in 1984, I have forgotten literally everything!!!
The team has grown together even more now. It is fun to attend classes. People are great. Shame is, by mid week this week, it will be over and we are all being dispersed into our units. So far I suspect the whole of the MET is probably a big team and I am sure it will be fun getting finally out and do some work.
Anyway, 3 more days left and a final exam.
And then we had 2 days of life saving training. That was extraordinarily good and important to have. Thinking about my last first aid training, which was back in 1984, I have forgotten literally everything!!!
The team has grown together even more now. It is fun to attend classes. People are great. Shame is, by mid week this week, it will be over and we are all being dispersed into our units. So far I suspect the whole of the MET is probably a big team and I am sure it will be fun getting finally out and do some work.
Anyway, 3 more days left and a final exam.
Sunday 16 August 2009
The Bill - Week 2
In week 2 we, the trainees, certainly became a team. This was particularly clear after 2 days of Officer Safety Training where we had to "get physical" and beat each other up, well, pretend to at least, so that we could learn how to defend ourselves. Admittedly, these 2 days were one of my best I have ever had. I was on a 2 day high, and my body must have released adrenalin like there was no tomorrow. Self-defence should be taught at schools I think, especially in London and other metropoles like this one. Our trainers are absolutely spot-on.
For the rest of the week we got our uniforms and learned several legal bits such as theft, offensive weapons, etc. We also had 2 exams - one in handcuffing techniques and the other one was an academic one and comprised all subjects taught so far. I managed to achieve 88% which is quite nice.
So, all in all, I still think joining the MET was the right thing to do. The training is absolutely fantastic, the curriculum enables us to learn all important matters in an extremely structured manner, and in fact, it is very funny and relaxed. Well done Training Department! Looking forward to week 3 now.
For the rest of the week we got our uniforms and learned several legal bits such as theft, offensive weapons, etc. We also had 2 exams - one in handcuffing techniques and the other one was an academic one and comprised all subjects taught so far. I managed to achieve 88% which is quite nice.
So, all in all, I still think joining the MET was the right thing to do. The training is absolutely fantastic, the curriculum enables us to learn all important matters in an extremely structured manner, and in fact, it is very funny and relaxed. Well done Training Department! Looking forward to week 3 now.
Sunday 9 August 2009
The Bill - Week 1
My first week passed by and I was extremely exhausted by the time Friday's lessons had finished. I went home and fell to bed and had a deep power nap. Saturday and Sunday I revised and did what I learned at university many, many years back - writing things up, summarizing pages and chapters from the big handout folder, and in the end, it was actually a very reasonable package to learn and review.
Last week we learned the "street" sections of PACE, the Police and Criminal Evidence Act - Stop & Search, Power of Arrest, etc. And then there was also a self-defence part one day which was my biggest challenge. But I think I mastered both parts pretty well.
Group dynamics is interesting. I am one of the oldest with my 39 years. Most people are in their early twenties. What is the best though about the group is its diversity - half men/half women, British, Continental European, and all sorts of racial mixes from around the globe which have integrated into Britain; like me, suppose. This is absolutely perfect and mirrors London's society extremely well.
What I find strange though, compared to Germany, the lack of a written Constitution enables British police to enter private living space only by applying PACE and without a warrant. This would be absolutely non-thinkable in Germany. The new policeman in me says "yes" to this right given by PACE, the German in me is still a bit hesitant to accept it.
All in all, I had an extraordinarily good experience, my class mates are pretty nice and friendly, and my trainers extremely funny and very professional. I am looking forward to week 2.
Last week we learned the "street" sections of PACE, the Police and Criminal Evidence Act - Stop & Search, Power of Arrest, etc. And then there was also a self-defence part one day which was my biggest challenge. But I think I mastered both parts pretty well.
Group dynamics is interesting. I am one of the oldest with my 39 years. Most people are in their early twenties. What is the best though about the group is its diversity - half men/half women, British, Continental European, and all sorts of racial mixes from around the globe which have integrated into Britain; like me, suppose. This is absolutely perfect and mirrors London's society extremely well.
What I find strange though, compared to Germany, the lack of a written Constitution enables British police to enter private living space only by applying PACE and without a warrant. This would be absolutely non-thinkable in Germany. The new policeman in me says "yes" to this right given by PACE, the German in me is still a bit hesitant to accept it.
All in all, I had an extraordinarily good experience, my class mates are pretty nice and friendly, and my trainers extremely funny and very professional. I am looking forward to week 2.
Monday 3 August 2009
The Bill
Today, a completely new chapter in my life is going to start - life as a policeman. And no, this is not a joke, but today and for the next 4 weeks I am going to get trained up in the police training facilities in north London and will then work in one of the boroughs on a voluntary basis, 16 hours a month minimum.
Most of my friends and family were asking me why on earth I would do that. There are a few reasons:
1. The Altruistic Reason: I truly believe everybody has to give something back to the community and society. We are all very good in taking and expecting, but giving can be an extremely interesting challenge, too, and it can be fun!
2. The Uniform Reason: I think I have always been fascinated by the police, from childhood on. Strangely enough, I never applied for a job with them when I still lived in Germany, but hey, one gets older and wiser.
3. The Professional Reason: Since I want to also establish myself as Executive Coach (besides my consulting career) I truly believe that getting trained and working as policeman will open my horizons immensely and add to my skill-set.
4. The Leisure Reason: I want to force myself to get out more and do something useful. Temptation is far too high to stay in and play with the computer, watch TV or just potter about when one could do something else.
5. The Social Reason: Extremely interesting to me is the possibility to get to know so many new and interesting people. Especially as freelancer one cannot get to know enough.
So, all in all, this makes sense to me. And I am looking forward to later on, on my Day 1.
Most of my friends and family were asking me why on earth I would do that. There are a few reasons:
1. The Altruistic Reason: I truly believe everybody has to give something back to the community and society. We are all very good in taking and expecting, but giving can be an extremely interesting challenge, too, and it can be fun!
2. The Uniform Reason: I think I have always been fascinated by the police, from childhood on. Strangely enough, I never applied for a job with them when I still lived in Germany, but hey, one gets older and wiser.
3. The Professional Reason: Since I want to also establish myself as Executive Coach (besides my consulting career) I truly believe that getting trained and working as policeman will open my horizons immensely and add to my skill-set.
4. The Leisure Reason: I want to force myself to get out more and do something useful. Temptation is far too high to stay in and play with the computer, watch TV or just potter about when one could do something else.
5. The Social Reason: Extremely interesting to me is the possibility to get to know so many new and interesting people. Especially as freelancer one cannot get to know enough.
So, all in all, this makes sense to me. And I am looking forward to later on, on my Day 1.
Sunday 2 August 2009
My Director
The other day I got a phone call from a colleague of mine from Proudfoot, it was Thomas, and he was my director on the Otto Bock project. We worked together on various other projects, too. It was the first time we chatted since 2005 I guess, which was really nice. There was no specific reason for the call, just a chat and touch base again. Thomas read this blog and whilst doing so, he recognised that I disgracefully left him completely out in the Otto Bock story! Shame on me!
Let me do that now and pay hommage to a team member (and no, he is not dead yet) who had an extremely vital role in the project. I especially need to thank him for all the client handling advice he gave me. As a young project manager, who is still green behind his ears, client handling (and I mean the top clients) is extremely vital.
In the worst of times when the savings had to be cashed in and defined he spent an extremely huge amount of time on the project and took a leading role. And I am very happy he did!
Anyway, I thought I still had to mention that.
Let me do that now and pay hommage to a team member (and no, he is not dead yet) who had an extremely vital role in the project. I especially need to thank him for all the client handling advice he gave me. As a young project manager, who is still green behind his ears, client handling (and I mean the top clients) is extremely vital.
In the worst of times when the savings had to be cashed in and defined he spent an extremely huge amount of time on the project and took a leading role. And I am very happy he did!
Anyway, I thought I still had to mention that.
Saturday 1 August 2009
A Sandwich nearly eaten...
Yesterday, 31st July, I finished the manuscript of my book. This so far final version has 49,000 words. I quite did not manage the last 1000 words to round things up, but am sure they will come at the next revision. I sent it out to a few friends who offered to edit it and check how good or bad it actually is. I am extremely grateful to all of them. I am in utter need of them as at the end of the day I wrote the book in English which is actually not really my mother tongue.
So, what is the next step? To be honest, I have absolutely no idea. On Twitter I am chatting to a few people who tell me different things - the one says I don't need an agent, the other one insists on agents. And publishing is absolute new to me. I read a book called "How to publish and make money from it" and she suggested to also go via an agent. I think I'll end up doing this, as agents are probably better in marketing the thing afterwards anyway.
Okay, that's an update so far. In the next month or so I will probably get the first reviews back, I will have to get in touch somehow with agents, professional editors, publishers and just take it from there.
I'll keep the world updated on the progress!
So, what is the next step? To be honest, I have absolutely no idea. On Twitter I am chatting to a few people who tell me different things - the one says I don't need an agent, the other one insists on agents. And publishing is absolute new to me. I read a book called "How to publish and make money from it" and she suggested to also go via an agent. I think I'll end up doing this, as agents are probably better in marketing the thing afterwards anyway.
Okay, that's an update so far. In the next month or so I will probably get the first reviews back, I will have to get in touch somehow with agents, professional editors, publishers and just take it from there.
I'll keep the world updated on the progress!
Monday 29 June 2009
The Cucumber Sandwich
Sorry for not updating my blog, but I am writing a book at the moment about my life in the UK. I guess it will be finished at some stage in July. And then I shall be back.
The book is called: "Dont mentschen ze var - a German on his Search for the Cucumber Sandwich".
The book is called: "Dont mentschen ze var - a German on his Search for the Cucumber Sandwich".
Thursday 4 June 2009
KPIs of SCP
SCP has a few KPIs by which one can see how well (or not so well) they have done.
Customer Service measured as Customer OTIF (On Time In Full). This KPI measures the orders a customer wants at what date with the ones actually delivered on that date. Whether these should be orders or order lines needs to be decided case by case.
Internal OTIF from factory to distribution centre (also called Factory OTIF). This is a shared KPI with SCO and measured the weekly planned orders with the actually produced orders which enter the distribution centre for distribution to the customers. This is more interesting in an MTS (Make To Stock) environment where SCP would be responsible for reorder points, safety stock, etc, as MTS orders are mainly generated by SAP or any other production planning system.
Stock. These stock KPIs can be expressed in total nominal stock value (raw material, finished goods, work in progress, packaging, goods for resale) or days of stock/inventory. Also, obsolete stock should be measured.
Customer Service measured as Customer OTIF (On Time In Full). This KPI measures the orders a customer wants at what date with the ones actually delivered on that date. Whether these should be orders or order lines needs to be decided case by case.
Internal OTIF from factory to distribution centre (also called Factory OTIF). This is a shared KPI with SCO and measured the weekly planned orders with the actually produced orders which enter the distribution centre for distribution to the customers. This is more interesting in an MTS (Make To Stock) environment where SCP would be responsible for reorder points, safety stock, etc, as MTS orders are mainly generated by SAP or any other production planning system.
Stock. These stock KPIs can be expressed in total nominal stock value (raw material, finished goods, work in progress, packaging, goods for resale) or days of stock/inventory. Also, obsolete stock should be measured.
Monday 1 June 2009
The Role of SCP (Supply Chain Planning)
The main task of SCP is to manage the forecast, plan and communicate, whereas it needs to be decided case by case to which amount and detail the planning part is to be undertaken.
I am perfectly happy with the minimum planning as in output planning, a wish list of which products need to be in the distribution centre at what date. Some planning departments also take over the whole of production planning (scheduling) as in scheduling which product needs to be produced at which line on what day, etc... I truly believe though that this kind of planning should remain within operations (more detail later).
Talking about communication, SCP should bundle the information which gets from the front end (sales and marketing) to operations. Nobody should be allowed to get in touch with operations but SCP.
And, SCP should manage the forecast of Sales and Marketing and allow operations (SCO) to plan resources.
I am perfectly happy with the minimum planning as in output planning, a wish list of which products need to be in the distribution centre at what date. Some planning departments also take over the whole of production planning (scheduling) as in scheduling which product needs to be produced at which line on what day, etc... I truly believe though that this kind of planning should remain within operations (more detail later).
Talking about communication, SCP should bundle the information which gets from the front end (sales and marketing) to operations. Nobody should be allowed to get in touch with operations but SCP.
And, SCP should manage the forecast of Sales and Marketing and allow operations (SCO) to plan resources.
Friday 22 May 2009
What if...?
What can happen if the operations department does actually do the thinking job and decides for themselves?
- Operations people normally think big, which means, the bigger the batch/lot size, the better for the fixed costs degression.
- They are not enough informed about the market and should solely concentrate on production/operations efficiency.
- Being focused on short term production results, they tend to neglect to look at the long term when it comes to planning and forecasting.
- Too many interfaces (inside and outside communication) distracts them from their real job - an efficient operation and delivery on time and in full.
There are more reasons, but these are the most important ones.
And now for future reference, when I say 'operations' or 'SCO', that actually means Supply Chain Operations. This is the department in the supply chain which "does" things, and that can be usually production, distribution, etc...
- Operations people normally think big, which means, the bigger the batch/lot size, the better for the fixed costs degression.
- They are not enough informed about the market and should solely concentrate on production/operations efficiency.
- Being focused on short term production results, they tend to neglect to look at the long term when it comes to planning and forecasting.
- Too many interfaces (inside and outside communication) distracts them from their real job - an efficient operation and delivery on time and in full.
There are more reasons, but these are the most important ones.
And now for future reference, when I say 'operations' or 'SCO', that actually means Supply Chain Operations. This is the department in the supply chain which "does" things, and that can be usually production, distribution, etc...
Thursday 21 May 2009
The Brains and the Hands
Talking Supply Chain I'd like to start with the model. Like in many areas it is advisable to separate the "brains" from the "hands", which means, don't let the doers decide what they should do and how much. That never ends up at an optimum.
In a project I am always open for suggestions and agree happily on some alterations to the model and tools which I intend to implement, but on that issue I categorically stay tough: NEVER LET PRODUCTION DECIDE WHAT, HOW MUCH AND WHEN THEY HAVE TO PRODUCE SOMETHING!!!
In a project I am always open for suggestions and agree happily on some alterations to the model and tools which I intend to implement, but on that issue I categorically stay tough: NEVER LET PRODUCTION DECIDE WHAT, HOW MUCH AND WHEN THEY HAVE TO PRODUCE SOMETHING!!!
Wednesday 20 May 2009
What's now?
What I generally do and did for my client: I would go to a business unit, and they are organised worldwide, analyse the situation, come up with recommendations for improvement, built a business case, and install the improvements. I mainly work in supply chain planning departments, factories and distribution centres.
The countries I have been involved with so far with this client: The Netherlands, Belgium, France, South Korea, China, Hungary, Poland and a tiny bit of UK.
What I want to do from now on in the blog is to write a bit more about the tools and methodology I used in the last couple of years.
Saturday 16 May 2009
Friday 15 May 2009
Nissan, the Team
We had one task force from Nissan during the 2 projects, Peter B (picture above). He was a very good guy and lived in Northamtpon. He knew the company pretty well and helped us installing our new management tools rather swiftly.
In the first project my consultant was Anne-Laure, and in the second one Javier.
Each project lasted for about 4 months.
The main issue was, Nissan was riddled with "cultural differences". There were the Spanish employees in the 2 sites in Spain, the British ones in Milton Keynes, and there were myriads of Japanese employees who were in Europe for a certain amount of time and also included in the project.
I do remember problems with the Japanese. They were language barriers and also no interest at all in any European project, as they were all very focused on directives from Japan.
Thursday 14 May 2009
Nissan Research and Development
One of my last projects with Proudfoot was the one at Nissan R&D in the UK, but with further 2 locations in Spain.
The project was about raising personal efficiencies of R&D directors, and in a second follow-up project a similar approach was rolled down to the supervisors.
The core product was to eliminate non-value added time and add more creativity to the European R&D department.
We did that through coaching, implementing a new "efficient meeting format" and e-mail etiquette. Each meeting was to be fedback and coaching to the chairmen given. The new e-mail formats ensured unity in writing e-mail across the European sites.
In special vision workshops we introduced them to the idea of new creativity at the workplace.
The project was about raising personal efficiencies of R&D directors, and in a second follow-up project a similar approach was rolled down to the supervisors.
The core product was to eliminate non-value added time and add more creativity to the European R&D department.
We did that through coaching, implementing a new "efficient meeting format" and e-mail etiquette. Each meeting was to be fedback and coaching to the chairmen given. The new e-mail formats ensured unity in writing e-mail across the European sites.
In special vision workshops we introduced them to the idea of new creativity at the workplace.
Saturday 9 May 2009
Mazda - Warehouse Management (2)
The warehouse project was actually pretty successful. We implemented fully fledged management systems in all their warehouses, trained management in management skills, implemented relevant KPIs, a planning tool and master schedule, supervisory shop floor tours... Well, the fully monty really.
I never thought I'd ever become an expert in warehousing and distribution. In a later project I was able to deepen my knowledge in that sector even further.
I never thought I'd ever become an expert in warehousing and distribution. In a later project I was able to deepen my knowledge in that sector even further.
Labels:
management systems,
management training,
Mazda,
warehouse
Friday 8 May 2009
Mazda - Warehouse Management (1)
Anyway, what we did with the warehouse section, we thorougly analysed them all. I think they had 5 throughout the country. They were all lacking the same: standards for each activity, good management, daily follow-up on the operation, no planning, no measurement of results... Basically, they had nothing and we had to start from scratch.
Thursday 7 May 2009
Mazda - Organisation
The organisational development bit turned out to be pretty difficult. What we did was to create an "Organisational Brown Paper" where we drew the current organisation in its rather detail.
We also had a list of all the salaries per department, so we could detect the cost per department (and the turn-over).
Then, we did the "green meadow approach", where we sat down and created the "new" organisation as if we were to establish a new company and we could use as many people from the "old" payroll as we wanted. We had several workshops, mainly with the directors and HR.
The final result was a suggestion for a new organisation. Initially, we did not sell the implementation of that new organisation, only a suggestion for a new one.
It sounds very easy, but the main problem was this HUGE resistance of literally everyone. I was greeted with hostility whenever I was spotted somewhere in the building. But we finally got it!
I had a task force. His name was Dominic. He was working as manager in one of their warehouses and he helped me with the organisation and the warehouses.
We also had a list of all the salaries per department, so we could detect the cost per department (and the turn-over).
Then, we did the "green meadow approach", where we sat down and created the "new" organisation as if we were to establish a new company and we could use as many people from the "old" payroll as we wanted. We had several workshops, mainly with the directors and HR.
The final result was a suggestion for a new organisation. Initially, we did not sell the implementation of that new organisation, only a suggestion for a new one.
It sounds very easy, but the main problem was this HUGE resistance of literally everyone. I was greeted with hostility whenever I was spotted somewhere in the building. But we finally got it!
I had a task force. His name was Dominic. He was working as manager in one of their warehouses and he helped me with the organisation and the warehouses.
Wednesday 6 May 2009
Mazda - Car Sales
In the car sales workstream we needed to deal with selling skills of car salesmen in those dealerships around southeast England.
It was a similar programme to the delicatessen one I managed - selling skills, upselling, more-selling. We trained them, played mystery shopper, had a training film, coached them, etc...
And as usual in projects like these it was a TTT approach, where we trained the trainer (TTT) and the trainer (the local car dealership managers) trained their sales staff. The board director was part of a film where he had to "send out the message" about the project, etc.
That whole workstream was pretty successful. I was only vaguely involved as my collage Judith was responsible for that work stream.
Unfortunately, I do not have too many pictures, in fact close to none, of this project.
It was a similar programme to the delicatessen one I managed - selling skills, upselling, more-selling. We trained them, played mystery shopper, had a training film, coached them, etc...
And as usual in projects like these it was a TTT approach, where we trained the trainer (TTT) and the trainer (the local car dealership managers) trained their sales staff. The board director was part of a film where he had to "send out the message" about the project, etc.
That whole workstream was pretty successful. I was only vaguely involved as my collage Judith was responsible for that work stream.
Unfortunately, I do not have too many pictures, in fact close to none, of this project.
Tuesday 5 May 2009
Mazda - UK!
After that year with Otto Bock, I finally got a project in the UK. My first proper job there since I started my career and moved to London. We are in the year 2002 now.
I was on a project in Tunbridge Wells, with a Mazda spinn-off. The project had 3 parts: car sales, organisational realignment and warehousing. My part was the organisation and the warehouses.
The client was a difficult one. The chairman was from Japan, there was an English CEO, and several English board members. There were constant frictions between chairman and CEO. I can talk that openly as this company does no longer exist.
The chairman was rather "tough" when it came to organisation, the CEO was more "soft" but also unreliable and sometimes with outbursts of verbal violence. A tough cookie!
The board of directors was also extremely difficult to deal with, especially my warehouse director.
I was on a project in Tunbridge Wells, with a Mazda spinn-off. The project had 3 parts: car sales, organisational realignment and warehousing. My part was the organisation and the warehouses.
The client was a difficult one. The chairman was from Japan, there was an English CEO, and several English board members. There were constant frictions between chairman and CEO. I can talk that openly as this company does no longer exist.
The chairman was rather "tough" when it came to organisation, the CEO was more "soft" but also unreliable and sometimes with outbursts of verbal violence. A tough cookie!
The board of directors was also extremely difficult to deal with, especially my warehouse director.
Monday 4 May 2009
Isle of Man
I have forgotten one project. The company was situated on the Isle of Man and produced kettle switches. It was an extremely peculiar project. The local director, a Welshman, had to sleep on a camping site as his company did not want to pay for a hotel; he also had to pay for his flights home every week or fortnight.
And what I have also learned, one ought to wave good-bye to the ferries leaving the island, otherwise it would bring back luck.
Our hotel, the poshest one in town, and an old Victorian one, was the draftiest place on earth with the worst service ever, and beds with mattrasses hanging through to the floor.
We were always scared on Friday afternoons that there was no storm, as otherwise Manx Airways would not leave the airport and we were caught on the island for the whole weekend. Scary thought.
The project as such was rather basic. It was a production project where we improved machine and labour efficiencies. I was responsible for the training and coaching.
One of the managers was a girl called Sue. She was from Liverpool. I had absolutely no clue whatever she said. I just sat there and happily smiled at her and nodded... ;-)
And what I have also learned, one ought to wave good-bye to the ferries leaving the island, otherwise it would bring back luck.
Our hotel, the poshest one in town, and an old Victorian one, was the draftiest place on earth with the worst service ever, and beds with mattrasses hanging through to the floor.
We were always scared on Friday afternoons that there was no storm, as otherwise Manx Airways would not leave the airport and we were caught on the island for the whole weekend. Scary thought.
The project as such was rather basic. It was a production project where we improved machine and labour efficiencies. I was responsible for the training and coaching.
One of the managers was a girl called Sue. She was from Liverpool. I had absolutely no clue whatever she said. I just sat there and happily smiled at her and nodded... ;-)
Friday 1 May 2009
Otto Bock - Final Thoughts
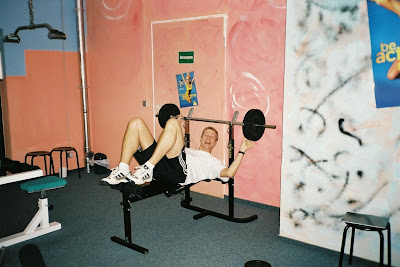
After all, and apart from those special "happenings", and even they were quite good in terms of learning experience, it was a great project. The client was satisfied, the core team was good, the location was nice, I learned a lot, and it formed me as project manager. So far it was my biggest single project, and also my most complex one. It was easy at times, sometimes very difficult, sometimes I wanted to quit my job. Overall, I loved it. And I feel privileged that I was able to be the manager of it.
Thursday 30 April 2009
Otto Bock - Dirty Laundry - 3
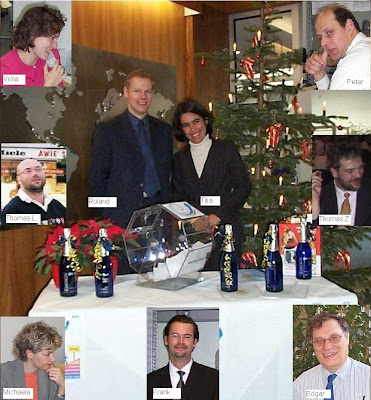
Well, "my victim" was as shocked as I was when we heard about that. It was a big thing. I cannot even tell anyone how devastated I was in those days. We had an idea - it was Christmas and we had a picture taken of the whole team; we created a special Otto Bock Team Christmas Card which we then sent around to "Proudfoot Worldwide", which means, thousands of recipients within the company got our Christmas wishes showing all of us happily next to each other.
That was such a relief when we sent that card out. And of course, that whole sexual harrassment thing was off the table.
I am wondering if I should delete this story, but then these things happen too and talking openly about it won't hurt.
Wednesday 29 April 2009
Otto Bock - Dirty Laundry - 2
My biggest problem was that I, as the most inexperienced PM, had to take on all those experienced ones, since their projects ran out and my company needed a place for them to work. Of course, the whole problem with "status" suddenly appeared. Some did have a huge problem to report into me.
One of them wanted my job and he started to gossip around that I would mob my team and suppress them and that I would not manage my client appropriately. He did not succeed, but his performance was outrageously bad. He was the most unmotivated person I have ever had on any of my projects. I tried to get rid of him, but one would not let me. Thank God, Tilia helped him in his area and she made up for his deficiancies. Tilia was great!!!
He also wanted to move to the US where he had a child. He was depressed about that, too. A short time after the project he was killed in an accident at a petrol station.
I hope his soul will rest in peace. He clearly did not lead a happy and fulfilled life.
One of them wanted my job and he started to gossip around that I would mob my team and suppress them and that I would not manage my client appropriately. He did not succeed, but his performance was outrageously bad. He was the most unmotivated person I have ever had on any of my projects. I tried to get rid of him, but one would not let me. Thank God, Tilia helped him in his area and she made up for his deficiancies. Tilia was great!!!
He also wanted to move to the US where he had a child. He was depressed about that, too. A short time after the project he was killed in an accident at a petrol station.
I hope his soul will rest in peace. He clearly did not lead a happy and fulfilled life.
Tuesday 28 April 2009
Otto Bock - Dirty Laundry - 1
Personally, the worst which happened to me were some of my colleagues. This project at times seemed to be like the cheap version of Dynasty or Dallas with so much backstabbing, intrigues, etc.
I am not mentioning any names, but this happened (Remember Sue Ellen from Dallas?):
One of my consultants turned out to be too interested in staying at the hotel bar in the evenings, and was not able to run his workshops in the morning with participants travelling from all over Germany. He had a good standing with the client and I was sort of relying on him. I covered up for him within my company, but also with the client. I would never ever do this again. Lesson learned!
There were a few more of those in my life to come actually. At least they never cancelled workshops but did their work.
I am not mentioning any names, but this happened (Remember Sue Ellen from Dallas?):
One of my consultants turned out to be too interested in staying at the hotel bar in the evenings, and was not able to run his workshops in the morning with participants travelling from all over Germany. He had a good standing with the client and I was sort of relying on him. I covered up for him within my company, but also with the client. I would never ever do this again. Lesson learned!
There were a few more of those in my life to come actually. At least they never cancelled workshops but did their work.
Monday 27 April 2009
Otto Bock - My Role as PM, Technical Experience
I just described, throughout the month, my technical experience. I learned so much. I especially benefited from supply chain management (production and planning), the balanced scorecard, and OTP with all those processes.
I was extremely lucky that this project was a "wall-to-wall" project, which means we did it all, the whole company. Gaining insight into that was extremely valuable, too.
And I learned a lot from all those other consultants on the project. Some, like Klaus, Edgar or Bernd, were specialists in their areas. I got my personal coaching sessions there.
The balanced scorecard was good since we did it really after the "scorecard bible" and not some Proudfoot-ised version.
It was absolutely great.
I was extremely lucky that this project was a "wall-to-wall" project, which means we did it all, the whole company. Gaining insight into that was extremely valuable, too.
And I learned a lot from all those other consultants on the project. Some, like Klaus, Edgar or Bernd, were specialists in their areas. I got my personal coaching sessions there.
The balanced scorecard was good since we did it really after the "scorecard bible" and not some Proudfoot-ised version.
It was absolutely great.
Sunday 26 April 2009
Otto Bock - My Role as PM cont'd
Things which don't kill you, only make you stronger!
This saying is so applicable when it comes to that project. I cannot even tell how much I learned - technically, personally, managerially and from a project management point of view.
Let's start with project management. Every week we had 2 TWNW Meetings, one with local directors and one with the 3 Cs (CFO, COO, CRO), who were our "top clients". In the local TWNW I let every area present something from the last few weeks. So, one week it was production, then sales, etc... It was the first time in company history that communication across interfaces was encouraged. I think those meetings were a big successs.
Then, internally with my consultants, I had "daily" reviews, which happened twice a week, and continuous one-to-ones with everyone. This sometimes also included the task forces.
The most important thing one has to do as PM is to communicate, even though it is pretty tough to do so and one needs to be disciplined.
My communication matrix had the following links: my company's headquarter in London, the office in Frankfurt, my director (who came about once or twice a week), my top clients, the directors, the worker's council, my consultants, the task forces, and of course every other one who wanted to talk to me.
This saying is so applicable when it comes to that project. I cannot even tell how much I learned - technically, personally, managerially and from a project management point of view.
Let's start with project management. Every week we had 2 TWNW Meetings, one with local directors and one with the 3 Cs (CFO, COO, CRO), who were our "top clients". In the local TWNW I let every area present something from the last few weeks. So, one week it was production, then sales, etc... It was the first time in company history that communication across interfaces was encouraged. I think those meetings were a big successs.
Then, internally with my consultants, I had "daily" reviews, which happened twice a week, and continuous one-to-ones with everyone. This sometimes also included the task forces.
The most important thing one has to do as PM is to communicate, even though it is pretty tough to do so and one needs to be disciplined.
My communication matrix had the following links: my company's headquarter in London, the office in Frankfurt, my director (who came about once or twice a week), my top clients, the directors, the worker's council, my consultants, the task forces, and of course every other one who wanted to talk to me.
Saturday 25 April 2009
Friday 24 April 2009
Otto Bock - My Role as PM
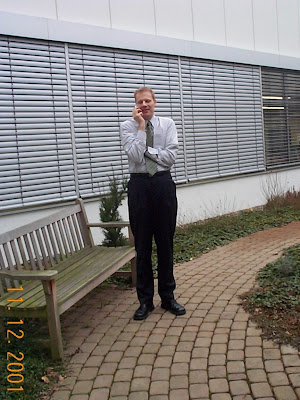
If you followed my blog so far, you know that I have only managed a project so far, and that was the Delicatessen producer Beeck, that sales enhancement project which lasted for 12 weeks and comprised of 24 manweeks. Basically, that was nothing compared to Otto Bock. The latter had about 250 manweeks and lasted for about a year.
The savings potential there was huge. I think I have already written about that.
So, there I was, this brandnew PM who had to manage the biggest project at that time. And the reason why it was me, I was the only native German speaker available.
In the aftermath, and even though I am glad I did it, but from a client point of view, this is a but unfair. Such a huge and important has deserved a more experienced PM.
One thing is for sure, in this project I learned to swim!!!
Thursday 23 April 2009
Otto Bock - R&D
R&D is the last area we developed. We basically streamlined the processes and implemented the gate management methodology.
This was mainly done by Klaus G. who used to work for Bayer many years ago in R&D and knew those processes pretty well. As far as I remember R&D went very well. Maybe one reason was that the R&D director, Dr H, was part of the executive team who wanted IMR (Proudfoot) to do the project.
There is nothing more to add. Unfortunately, I have no photo stored for that.
In the next few blog entries, I want to write a bit more about myself and how I managed the project, etc.
This was mainly done by Klaus G. who used to work for Bayer many years ago in R&D and knew those processes pretty well. As far as I remember R&D went very well. Maybe one reason was that the R&D director, Dr H, was part of the executive team who wanted IMR (Proudfoot) to do the project.
There is nothing more to add. Unfortunately, I have no photo stored for that.
In the next few blog entries, I want to write a bit more about myself and how I managed the project, etc.
Friday 17 April 2009
Otto Bock - Sales (Front End, Sales)
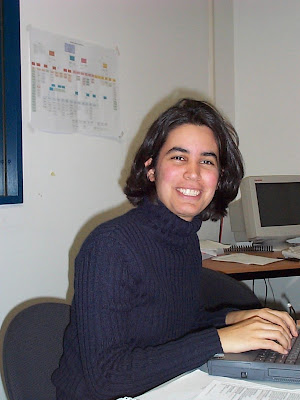
In the Sales department we implemented a management system comprising meeting structure, KPIs, etc. There was also a re-organisation in that department and a new director took over. We worked on the sales process, selling techniques, but did not roll out something like my project before. Again, main focus was order entry as this was the most vital issue for the new director.
Labels:
management systems,
Otto Bock,
sales,
sales enhancement
Thursday 16 April 2009
Wednesday 15 April 2009
Otto Bock - Sales (Front End)
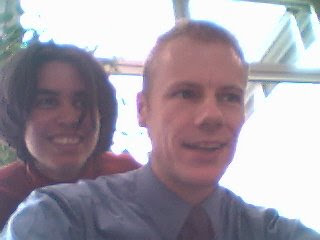
Another big work stream was the Front End, which is basically Sales and Order Entry.
Responsible for this workstream were mainly Peter and Tilia. Peter was a project manager and Tilia a senior consultant.
I remember we pinned down all the processes there, especially the order entry one. This one was vital, as it gave the input for production and the rest of the supply chain.
We had difficulties with the manager of order entry. She was somewhat stubborn and even her superiors had problems dealing with her. She was very convinced that her processes were pretty perfect. One day, we took her to another company which is also in the healthcare sector and produces similar products (the Sales director knew the CEO there) and showed her a different way of how order entry can be done, in fact more effectively and efficiently.
Order entry is extremely crucial, as prosthetics and wheelchairs are "tailor-made" items and each patient has own personal requirements. There are millions of ways a wheelchair can be composed.
Tuesday 14 April 2009
Otto Bock - Subsidiaries
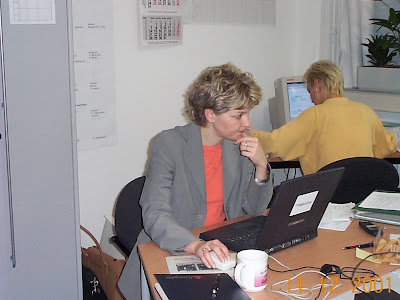
I already mentioned that Viola was responsible for one subsidiary. The company had another one though, in Rhineland-Palatinate. This was the responsibility of Michaela who was also heavily involved in production and R&D.
She implemented the management system we developed for the headquarter - action corners, shop-floor controls, etc.
Proudfoot in those days went through another merger and bought an Austrian company called Czipin & Partner. Michaela and Tilia were from there. Our project was the only one in the world which combined people from all 3 companies - (original) Proudfoot, IMR and Czipin.
Monday 13 April 2009
Sunday 12 April 2009
Otto Bock - Suggestion Box
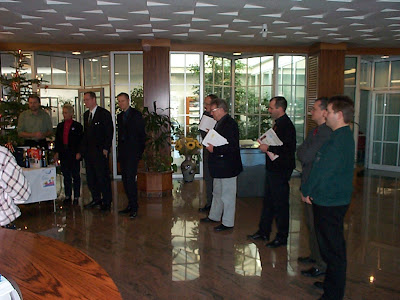
I have forgotten what we called the programme, but we also implemented a suggestion box where employees could unload their problems with or without suggestions for improvement.
We had a specific team among the task force to deal with the entries. The best ones got prizes. On the picture left is the prize draw.
I think we were pretty successful. We got lots of entries, and some of them with good potential for improvement.
From the consultants it was Tilia who dealt with the programme. She did an excellent job.
Saturday 11 April 2009
Otto Bock - Balanced Scorecard (2)
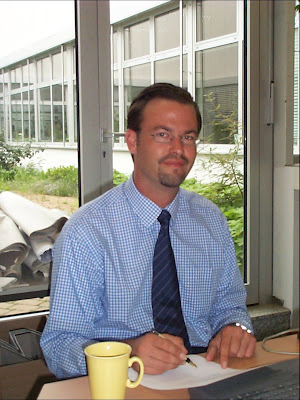
I must congratulate Frank for his BSC implementation and development. He did an extremely good job thinking about that he did not have any experience with BSC. Neither of us really had. We had to get the original Kaplan & Norton book and implemented it the way it has been suggested there.
Implementing a measurement system was our daily business and we all knew how to do it, but linking those indicators to strategic targets was something we have never done. We and the client did not even know in those days what the short-, medium-, and long-term targets were. Those had to be defined first.
Implementing a BSC takes quite a while if doing it right and with the methodology suggested. But once it is done, it is amazing what a fabulous tool it actually is.
Anyone who wants to know how to implement it, please get in touch. Going into detail here on my blog would be too much.
On the photo is Frank again.
Friday 10 April 2009
Otto Bock - Balanced Scorecard (1)
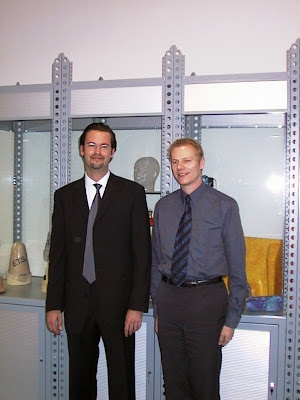
One other area for us was the Balanced Scorecard which we installed. A balanced scorecard is defined as this (Wikipedia):
"The Balanced Scorecard (BSC) is a performance management tool which began as a concept for measuring whether the smaller-scale operational activities of a company are aligned with its larger-scale objectives in terms of vision and strategy.
By focusing not only on financial outcomes but also on the operational, marketing and developmental inputs to these, the Balanced Scorecard helps provide a more comprehensive view of a business, which in turn helps organizations act in their best long-term interests."
By focusing not only on financial outcomes but also on the operational, marketing and developmental inputs to these, the Balanced Scorecard helps provide a more comprehensive view of a business, which in turn helps organizations act in their best long-term interests."
We used the original approach as developed by Norton and Kaplan in 1992.
On the picture one can see Frank and myself (and no, I did not train to enter the army). Frank was responsible for the balanced scorecard implementation.
Thursday 9 April 2009
Otto Bock - OTP Installation again
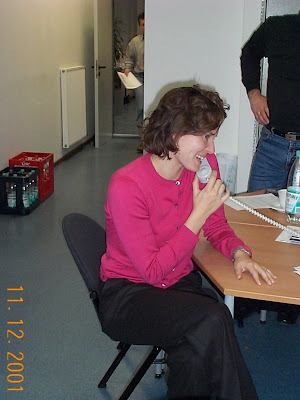
I have one more picture of Viola and thought I can write one more entry about OTP.
Her main fields, apart from the overall OTP process, were logistics and one of the subsidiaries (the location in Thuringia in which they produced wheel chairs).
In logistics, which was mainly warehousing, Viola managed to cut down throughput time and work with an extremely difficult manager who was not easy to deal with. It was an effective combination of charm and professionalism.
In the production subsidiary she implemented the management control system we also installed in the headquarters.
I need to say, Viola was one of my best consultants on the job. She lives in London now, and I should get back in touch at some stage.
Wednesday 8 April 2009
Otto Bock - OTP Installation
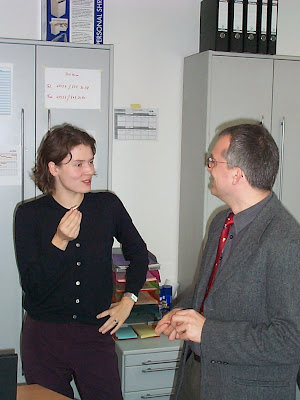
OTP is an interesting workstream as it comprises all other areas of the project, apart from R&D which we also looked at.
Viola's interfaces were mainly with the workstreams sales, order entry, production, logistics, payment control, whereas the latter 2 were her own areas.
OTP basically works like this: All major processes should be mapped and critiqued. Times of sub-proceses should be taken to understand how long "the average" process takes.
And then, after those critique sessions, improvement plans have to be developed and implemented. Best would be to do this with the 6 Sigma methodology, but in those days we decided not to.
After the improvements have been implemented, new standard times have to be taken and financial savings calculated.
On the pictures is Viola and her task force, who luckily was also responsible for ISO.
Tuesday 7 April 2009
Otto Bock - OTP
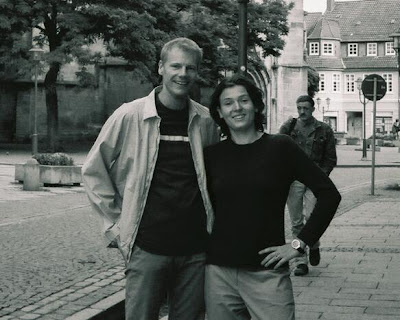
The other big workstream was OTP (Order to Payment) which covered the whole value chain throughout the company, starting with the incoming customer order, ending with the customer payment.
Poor Viola was responsible for that one. Her task was to do a hell of a lot of process mapping. Brown Papers must have grown out of her ears.
But she has done an extremely good job. With all those processes in mind, she probably knew the company the best.
Monday 6 April 2009
Otto Bock - Layout
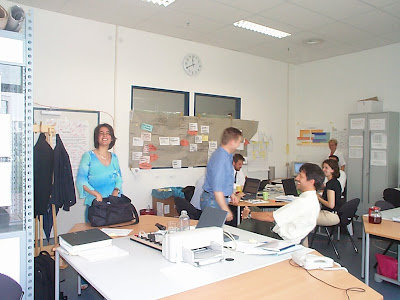
It was the biggest project Proudfoot at that time. We sold €9m of financial savings, the project cost €3m, which, I think, equalled up to about 200-something manweeks. It was a HUGE project. In our peak period we were up to 12 consultants and 15 task forces.
I'll talk more about each workstream in the following entries.
ON the photo one can see our "birdroom", the project room.
Sunday 5 April 2009
Otto Bock - Production (3)
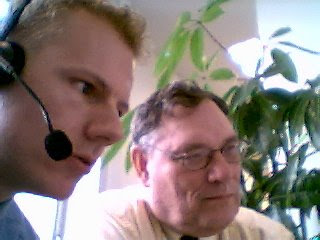
In the end, and as far as I remember, we managed to split planning from production, and also got the disciplines installed. Bernd was hired as production manager and the old one sent into his pension.
What we did not manage was to lay off the surplus workers. But this was due to political reasons.
With the management system we implemented they finally could talk about real issues and take actions accordingly.
On the photo is Edgar and myself. In those days we got a web-cam as the latest thing to have. We were supposed to talk to headquarters with it from then on. We installed it, but in fact, never used it.
Saturday 4 April 2009
Otto Bock - Production (2)
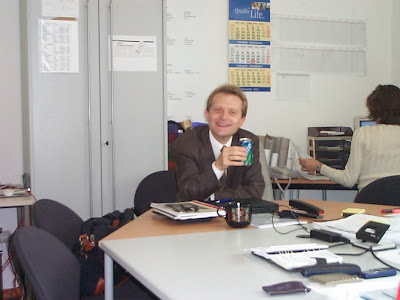
The production director was not overly cooperative, especially when it came to segregating planning from production. He saw that would be a loss of power. I always had the feeling he was "sitting it out", hence waiting till the project was over and then go back to the old ways.
The Otto Bock production process was extremely difficult and I have never ever seen anything like that again. In the usual scenario there are 2 or so production steps (imagine, food and chemical industry with mixing and filling as those 2 steps), but talking artificial limbs, those steps are enormous. There were workshops for wood, metal, and when talking metal, there was a smith, welding, etc, then there was a rubber part (the the fake skin), etc. So, the logistics within production alone was a nightmare for planning. Bear in mind, standards were not defined.
We implemented a management control system, supervisory shop-floor tours, action corners in order to display and discuss daily results and action variances, etc.
On the photo one can see our consultant Bernd who was responsible for production after Thomas left the team.
Friday 3 April 2009
Otto Bock - Production (1)
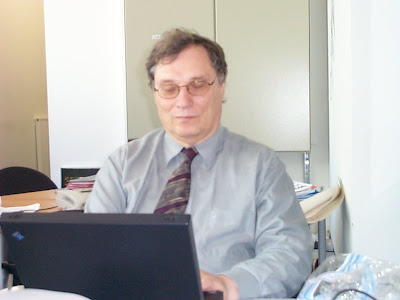
The main 2 problems production had were:
i) the production department was also responsible for planning,
ii) SAP standard hours were missing or wrong.
These 2 are the main 2 production problems which I have found in my career so far. Production is like a monster, it is always hungry and wants big portions, hence the batch sizes tend to get bigger and bigger and measurement is only done in kg, as this shows a good productivity. Productivity is a measure of volume/hours.
And talking about SAP standards, whenever SAP is being introduced, standard hours seem to be estimated rather than thoroughly measured. Of course, once one puts estimates in it, the planning function of SAP and any other production planning tool is completely out of order.
i) the production department was also responsible for planning,
ii) SAP standard hours were missing or wrong.
These 2 are the main 2 production problems which I have found in my career so far. Production is like a monster, it is always hungry and wants big portions, hence the batch sizes tend to get bigger and bigger and measurement is only done in kg, as this shows a good productivity. Productivity is a measure of volume/hours.
And talking about SAP standards, whenever SAP is being introduced, standard hours seem to be estimated rather than thoroughly measured. Of course, once one puts estimates in it, the planning function of SAP and any other production planning tool is completely out of order.
On the photo is Edgar. He was part of the production team and dealt with the master schedule and trained consultants and task forces.
Thursday 2 April 2009
Otto Bock - The PLUS Team
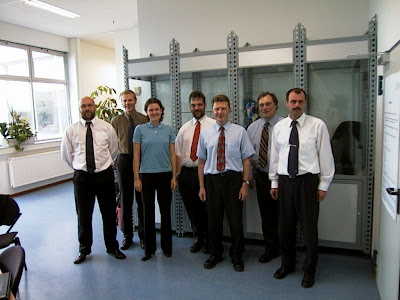
We called the project PLUS, which stands for (in German) "Prozesse, Logistik und Systeme".
Since we needed to make sure that key staff and management could take over once the project has finished we selected and trained several task forces. The main task force was a guy called Hubert. He was a very good person, very open, but a bit nervous. At peak times we had up to 15 task forces, whereas the main and full-time ones were 7 I think.
On this photo are Thomas, myself, Viola, Thomas, Emmanuel, Edgar and Hubert. Apart from Hubert the rest was from Proudfoot.
I think this photo was taken for a company publication in the very beginning before we selected the task force team.
Wednesday 1 April 2009
Otto Bock - The Analysis (2)
This company never went through any consulting projects and it showed in their processes and studies. It was an unmarked landscape so to speak.
Their main processes were inefficient, long-winded and not harmonised with each other, people lacked training, they did not produce what the market needed, not in time anyway, stocks were high, we detected silo mentality between departments, there were no real KPIs to steer the company, R&D processes were not managed well, new products developed, old ones never deleted, and so on and on and on... Not to talk about that they had far too many people work for them.
We presented those findings and a project plan and it got accepted. The biggest project Proudfoot-worldwide in those days was sold.
Their main processes were inefficient, long-winded and not harmonised with each other, people lacked training, they did not produce what the market needed, not in time anyway, stocks were high, we detected silo mentality between departments, there were no real KPIs to steer the company, R&D processes were not managed well, new products developed, old ones never deleted, and so on and on and on... Not to talk about that they had far too many people work for them.
We presented those findings and a project plan and it got accepted. The biggest project Proudfoot-worldwide in those days was sold.
Tuesday 31 March 2009
Otto Bock - The Analysis (1)
As usual, before a project starts we were tasked to do an analysis. They told me I was the designated project manager as I was the only one available who was a German native speaker. The project was supposed to be massive. I remember I was thrilled, scared, and excited at the same time.
The analysis was hell on earth. All of the consultants and I just hated it. Every day we slaved away for about 20 hours - DILOs, Brown Papers, interviews, and further studies, studies, studies... It was all not very well organised and we were never asked for our opinion and just had to deliver studies to feed the analyst.
Good news was, it was a strong team building exercise for us consultants. We stuck together and endured. The consultants told me I'd be a good PM running the show and they hoped I'd get it. At that time I was not overly sure if I wanted it anymore....
The analysis was hell on earth. All of the consultants and I just hated it. Every day we slaved away for about 20 hours - DILOs, Brown Papers, interviews, and further studies, studies, studies... It was all not very well organised and we were never asked for our opinion and just had to deliver studies to feed the analyst.
Good news was, it was a strong team building exercise for us consultants. We stuck together and endured. The consultants told me I'd be a good PM running the show and they hoped I'd get it. At that time I was not overly sure if I wanted it anymore....
Labels:
Analysis,
Business Review,
Otto Bock,
Project Manager,
Project team
Monday 30 March 2009
Otto Bock - The Client
Otto Bock is a company that produces artificial limbs, wheelchairs, orthopaedic tools, etc. It is probably the best company worldwide in their field, especially when it comes to prosthesis. If one sees runners at the Paralympics, one can be assured that those artificial legs were produced by Otto Bock. From that point of view, the company is absolutely top notch.
All the knowledge I have dates back to the early 2000s, hence things might have changed. The company is privately owned and situated in Lower Saxony at the border to former East Germany. It is basically in no man's land.
We hardly ever saw the owner, but he had an executive team running the show and the project as steering committee - first 2 directors and then a further one who was newly hired.
All the knowledge I have dates back to the early 2000s, hence things might have changed. The company is privately owned and situated in Lower Saxony at the border to former East Germany. It is basically in no man's land.
We hardly ever saw the owner, but he had an executive team running the show and the project as steering committee - first 2 directors and then a further one who was newly hired.
Sunday 29 March 2009
Otto Bock - The Start
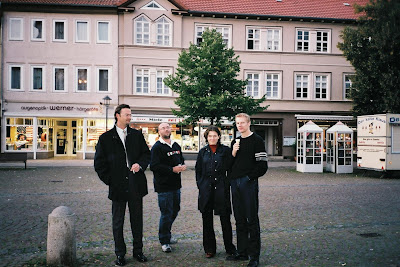
Otto Bock is my most interesting project I have ever managed. In that project I got it all, extremely interesting work streams, a big team to manage, a good client, and colleagues who challenged my social and project management skills to the very edge of endurability.
My last project took me already 8 blog entries, be prepared to read throughout most of April about this one.
To start with a picture of the core team of consultants who were on the project from day 1 - Frank, Thomas, Viola and myself.
Saturday 28 March 2009
Selling Wine
This delicatessen project was quite a success, especially within Proudfoot, as we have completely rewritten and remodelled that selling skills manual they had. There was a very small project at the time, it was a vineyard in Germany, that also needed selling skills.
I was assigned to that project for a few weeks and implemented a similar programme there. This project was a very strange project, as it was more like a private coaching project for the son and heir of the vineyard rather than getting some selling skills across and the project manager was not overly happy about it.
I think the son was extremely strange and what he really needed was professional care rather than management coaching. Oh well, not for me to judge. I did my thing and on one day I got a call to move over to my biggest challenge so far - a company called Otto Bock.
I was assigned to that project for a few weeks and implemented a similar programme there. This project was a very strange project, as it was more like a private coaching project for the son and heir of the vineyard rather than getting some selling skills across and the project manager was not overly happy about it.
I think the son was extremely strange and what he really needed was professional care rather than management coaching. Oh well, not for me to judge. I did my thing and on one day I got a call to move over to my biggest challenge so far - a company called Otto Bock.
Labels:
coaching,
sales enhancement,
selling skills,
vineyard
Friday 27 March 2009
Thursday 26 March 2009
Wednesday 25 March 2009
Salmon, Shrimps and Krautsalad (6)
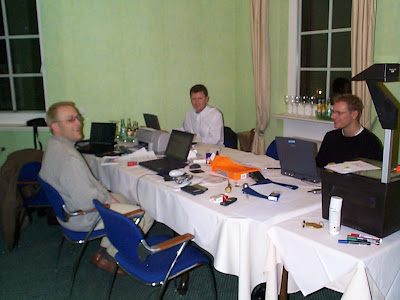
And then, finally, after the management system was ready to go and the managers trained and trainers and coaches we needed to tour the country (all 4 sales regions) and train, train, train...
And I must say, the area sales managers did all an extremely good job. I was rather impressed.
Labels:
Project Manager,
sales enhancement,
selling skills,
skills
Tuesday 24 March 2009
Salmon, Shrimps and Krautsalad (5)
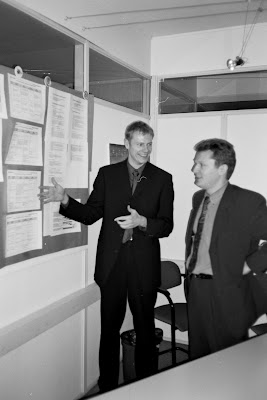
So, using skills methodology we would not train the sales representatives ourselves, but we left that for the area managers to do. We trained those area managers though in how to train their employees.
So, staying within the methodology, the TTTs were for us to train the area managers as trainers (Train the Trainer), whereas the area managers trained their staff in TTE sessions (Train the Employee).
So, staying within the methodology, the TTTs were for us to train the area managers as trainers (Train the Trainer), whereas the area managers trained their staff in TTE sessions (Train the Employee).
After the training we designed coaching sessions where the area sales managers were tasked to go randomly on tour with their staff and give coaching. TTCs were the Train the Coaches sessions in which we trained the area managers in how to coach, and in CTCs we coached them in their coaching effort. This system was waterproof.
Subscribe to:
Posts (Atom)